Estrategias que transforman su empresa, aumentan los ingresos, productividad, compromiso y deleitan a los clientes.
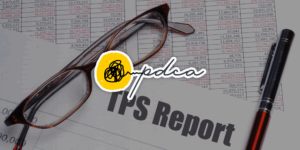
Guía Esencial para Líderes: Optimiza tu Manufactura con el TPS
Cuando inicias con el Sistema de Producción de Toyota (TPS), un método probado para optimizar la manufactura, es fácil cometer errores que parecen lógicos pero sabotean tus resultados. Este sistema, desarrollado por Toyota en los años 50, transformó la industria con principios como mejora continua y eliminación de desperdicios. Aquí te mostramos los 5 errores más comunes que los principiantes cometen al implementar el TPS y cómo evitarlos para lograr una manufactura eficiente.
1. Automatizar Procesos Ineficientes Antes de Optimizar
Automatizar suena atractivo, pero es un error grave si los procesos son ineficientes. Si automatizas un desperdicio, solo acelerarás el problema, aumentando costos y retrasos.
Cómo Evitarlo
Estandariza y mejora los procesos primero. Toyota priorizó ajustar flujos antes de implementar tecnología, logrando un impacto real en eficiencia.
2. Enfocarse Solo en las Herramientas del TPS
Técnicas como 5S (orden y limpieza), Kaizen (mejora continua) y mapeo de flujo de valor son esenciales, pero centrarte solo en ellas sin construir una cultura de cambio limita los resultados.
Cómo Evitarlo
Fomenta una mentalidad de mejora continua. Las herramientas del TPS deben ir acompañadas de compromiso organizacional para generar impacto sostenible.
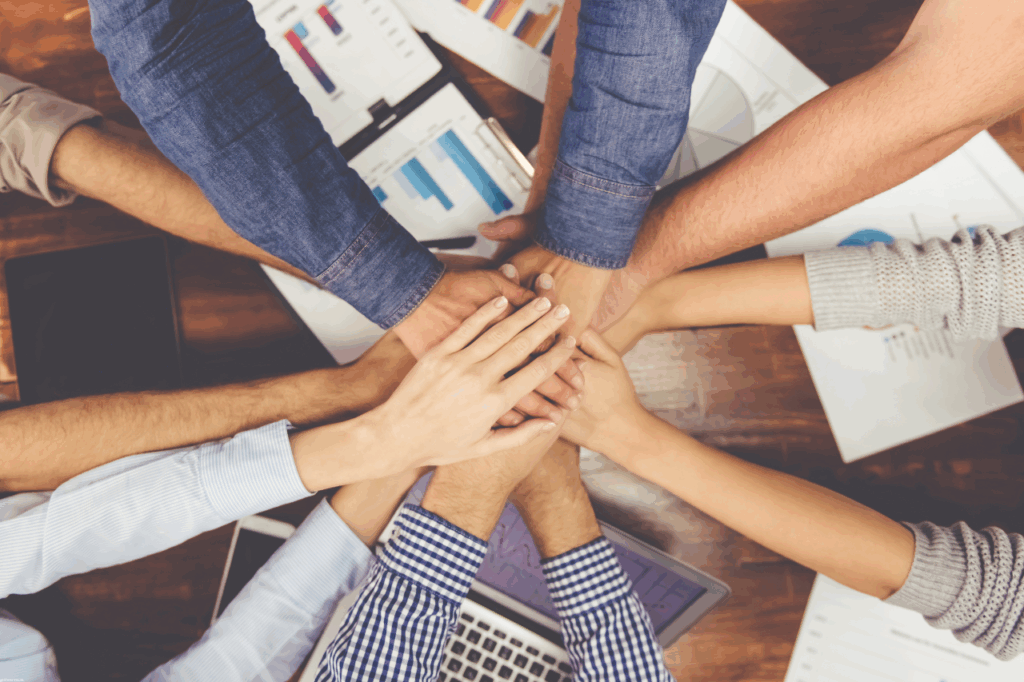

3. Imponer el TPS Sin Involucrar al Equipo
Los operarios conocen los cuellos de botella mejor que nadie. Imponer el TPS sin escucharlos genera resistencia y frena el cambio.
Cómo Evitarlo
Involucra a tu equipo desde el inicio. Toyota integró las ideas de sus operarios en el TPS, logrando una adopción exitosa y sostenible.
4. Buscar la Perfección en Lugar de Mejoras Constantes
Esperar soluciones perfectas paraliza el progreso. El TPS se trata de avanzar paso a paso, no de alcanzar la perfección de inmediato.
Cómo Evitarlo
Prioriza mejoras diarias pequeñas. Toyota demostró que un avance del 1% diario supera un plan ambicioso nunca ejecutado.
5. Esperar Resultados Sin un Liderazgo Comprometido
Si los líderes no impulsan la mejora continua con el ejemplo, el TPS será solo teoría sin impacto real.
Cómo Evitarlo
Los líderes deben modelar los principios del TPS. Taiichi Ohno, pionero del TPS, lideró con el ejemplo, asegurando su éxito en Toyota.
Transforma tu Manufactura con el TPS, el Sistema de Producción de Toyota no es magia, sino sentido común bien aplicado. Evita estos errores y optimiza tu manufactura con un enfoque práctico. ¿Listo para implementar el TPS sin tropiezos? Contáctanos para asesorías personalizadas y lleva tu operación al siguiente nivel.